TUNGSTEN FURNACE : AN OVERVIEW
The tungsten vacuum furnace is an advanced and adaptable thermo vacuum equipment that has transformed numerous sectors, ranging from aerospace and defense to metalworking and research. Tungsten vacuum furnaces are specially engineered to generate a controlled environment devoid of impurities, with vacuum levels reaching up to 10 -5 mbar and temperatures as high as 3000 degrees Celsius. Tungsten, a metal of strategic significance, possesses several remarkable properties. It exhibits an exceptionally high melting point of 3410°C, a density of 19.26 g/cc, and exceptional mechanical strength at elevated temperatures. Additionally, tungsten demonstrates superior thermal stability, excellent shielding capabilities against gamma radiation, and commendable electrical and thermal conductivity. The tungsten vacuum furnace finds utility in diverse sectors including aerospace and defense, metalworking, research and development, and more. Its adaptability enables accurate temperature control, controlled atmospheres, and efficient heating and cooling processes. Consequently, it proves to be an invaluable asset in applications such as heat treatment, brazing, melting, and annealing. The proposed tungsten furnace considered in this project is for Bhabha Atomic Research Centre, Mumbai, India, intended for various metallurgical and research applications, developed by Hind High Vacuum (HHV) Group, a leading vacuum technology company based in Bangalore, India.

OUR ESTEEMED CLIENT
Our valued client, Hind High Vacuum (HHV) Group, is a leading thin film and vacuum technology group in India. With nearly six decades of experience, HHV specializes in designing and manufacturing high vacuum equipment for both research and industrial purposes. Currently, HHV is working on the development of a Tungsten vacuum furnace for the Bhabha Atomic Research Centre, catering to various metallurgical applications. To ensure the success of this project, HHV has sought the expertise of Niharika Computational Engineering Solutions Pvt Ltd (NCES). NCES will provide professional consultancy services in the field of theoretical heat transfer calculations and Computational Fluid Dynamics (CFD) analysis. This collaboration aims to evaluate the thermal performance of the proposed tungsten furnace, ensuring its efficiency and effectiveness. By leveraging NCES's knowledge and experience in heat transfer calculations and CFD analysis, HHV aims to optimize the design and functionality of the tungsten furnace. This partnership highlights HHV's commitment to delivering high-quality and innovative solutions to its clients in the field of vacuum technology.
THEORETICAL HEAT TRANSFER CALCULATIONS
Thermal hand calculations are of utmost importance in enhancing the design and functionality of thermo vacuum systems. These calculations enable engineers to gain a deeper comprehension and analyze the heat transfer mechanisms within the thermo vacuum system, resulting in enhanced efficiency. Through precise predictions of heat transfer rates, temperature distributions, and thermal gradients, engineers can optimize the thermal chamber, insulation, and heating element configuration to achieve maximum efficiency.
COMPUTATIONAL FLUID DYNAMICS (CFD) ANALYSIS
Computational Fluid Dynamics (CFD) is a computational method employed to simulate and examine the behavior of fluid flow and heat transfer phenomena. Through the division of the computational domain into smaller control volumes, CFD computes and solves the governing equations for fluid flow and heat transfer, taking into account different boundary conditions and physical properties. This enables engineers to anticipate fluid flow patterns, temperature distributions, and pressure drops within intricate systems, eliminating the necessity for costly and time-consuming physical prototypes. Additionally, CFD analysis provides the means to visualize and comprehend fluid flow behavior, facilitating the identification of potential design flaws and optimization prospects.
CFD MESH
The CFD mesh for the tungsten furnace comprises 8 million tetrahedral elements, adhering to the mesh quality index specified by industry standards. The mesh is finely resolved in areas with high thermal gradients.
CFD MODELLING
The physics is modeled as 3D, steady state. Radiation is modeled with surface-to-surface (S2S) radiation enclosure model. Material properties and boundary conditions are applied accordingly, taking into account constant interaction with both the HHV Engineering team and the Engineering team of vendors who provided sub-systems to HHV.
The primary focus of the study revolves around analyzing the Temperature field, temperature gradient, radiative heat fluxes on different surfaces, and a comprehensive heat balance sheet that quantifies the flow of heat energy throughout the entire system.
We Got More
Go through All Our Case Studies
CFD analysis of Rotary Vacuum Brazing Furnace (RVBF)
RVBF is an Inert gas-circulated, closed-loop Integrated thermal system with operating temperatures up to 1500 Deg Celsius. The Integrated thermal loop consists of a heat treatment chamber, a centrifugal blower for gas circulation, Shell and Tube Heat exchanger to achieve gas cooling, and an Electromagnetic Induction heater to reach a higher operating temperature. Controlled cooling of the job is essential to achieve the desired metallurgical structure after heat treatment. Niharika Computational Engineering Solutions Pvt Ltd (NCES) has collaborated with the client and analyzed the overall thermal performance of RVBF. We conducted transient Computational Fluid Dynamics (CFD) analysis to analyze the cooling of the job during the cooling cycle. Our CFD analysis process is validated with the help of experimental data obtained from the existing RVBF unit, which is of slightly lower capacity. Read More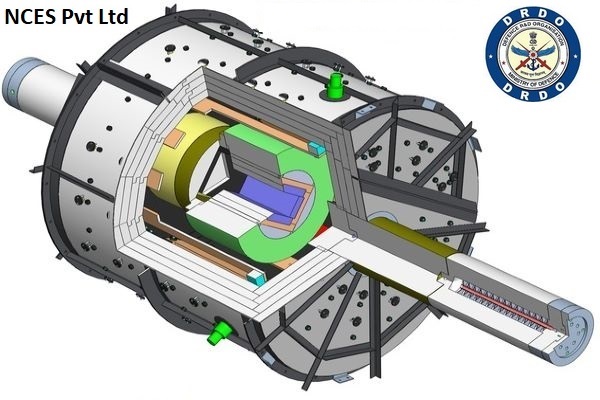
Thermal and structural analysis of Chemical Vapor Infiltration (CVI) and Chemical Vapor Deposition (CVD) furnace
CVI and CVD is a thermo-vacuum chamber operating up to 2500 Degree Celsius. CVI-CVD furnace is mainly to mold high-temperature sustainable composites used in supersonic missiles. This Thermo-vacuum facility is commissioned at DRDL- Hyderabad, the Defence Research and Development Organization (DRDO) propulsion complex, Ministry of Defence, Government of India. The electromagnetic Induction heater is used to generate higher operating temperatures of the order of 2500 Degree Celsius. Niharika Computational Engineering Solutions Pvt Ltd (NCES) has collaborated with the client and conducted Computational Fluid Dynamics (CFD) analysis to assess the thermal performance of the furnace. We also conducted structural analysis (FEA) to predict the thermal expansion of the plunger unit. Read More
Thermal analysis of Landing gear magnetic brake disk
Magnetic brake is a direct replacement for the current state-of-the-art carbon brakes. The magnetic brake can recapture a significant portion of the aircrafts kinetic energy during the landing. In this project, we carried out CFD analysis for the aircraft landing brake for a range of decelerating speeds. Our scope of work is to calculate the heat dissipation during the landing of the aircraft and conduct thermal analysis to estimate the temperature developed on the critical components of the braking system, which further helps the designer choose a suitable cooling mechanism. Hexahedral mesh is generated for the CFD domain, and CFD analysis is carried out using the Multiple Reference Frame Model (MRF). Read MoreCFD and structural analysis of Digital aircraft engine controller-FADEC
FADEC is a computer-managed aircraft ignition and engine control system used in modern commercial and military aircraft to control all aspects of engine performance digitally. Our client is a Government of India-approved aerospace and defense R&D unit. The client is developing FADEC for Defence Research and Development Organization (DRDO), Ministry of Defence, Government of India. We collaborated with the client from the initial stages of the design process. Our domain expertise leveraged with Computational Fluid Dynamics simulation (CFD analysis) technology has accelerated our clients Innovation process. We performed modal analysis, Vibration, Sine sweep, Random vibration analysis, Shock analysis, and Acceleration analysis per military standards (MIL-Std 810H) using Finite Element Analysis (FEA)software. Our meticulous engineering practices yielded reliable analysis results, which enabled our client to explore more design options and make well-informed decisions at the appropriate stages in the product development cycle. Read More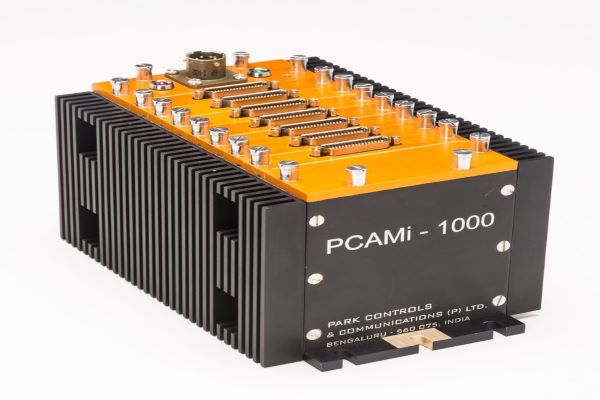
CFD and Structural analysis for Telemetry Flight Test Instrumentation
PCAMI-1000 is an Airborne ruggedized Instrumentation System that handles excitation, attenuation, signal conditioning, data, embedded video and audio acquisition, encoding, operating numerous buses such as MIL 1553 and Arinc, and onboard data recording and data transmission with chassis of varied slot capacities such as 3, 6, 9 and 13 slots. Our client is a Government of India-approved aerospace and defense R&D unit. We collaborated with the client from the initial stages of the design process. Our domain expertise leveraged with Computational Fluid Dynamics simulation (CFD analysis) technology has accelerated our clients Innovation process. We performed modal analysis, Vibration, Sine sweep, Random vibration analysis, Shock analysis, and Acceleration analysis per military standards (MIL-Std 810H) using Finite Element Analysis (FEA)software. Our meticulous engineering practices yielded reliable analysis results, which enabled our client to explore more design options and make well-informed decisions at the appropriate stages in the product development cycle. Read More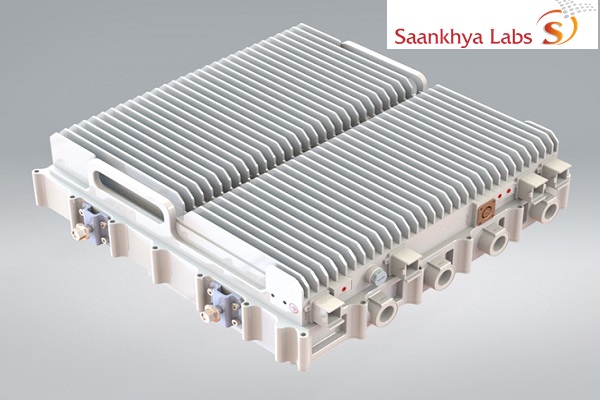